Navigating Mine to Wire
The "Mine to Wire" manufacturing process refers to the comprehensive journey of electrical conductors, from the extraction of raw materials in mines to the final production of wires. This intricate value chain involves several stages, each with specific tasks and considerations.
The manufacturing process involves a meticulous journey from the extraction of raw materials through refining, alloying, conductor manufacturing, quality control, and final product assembly.
This comprehensive approach ensures the production of high-quality electrical conductors that meet the stringent requirements of diverse applications.
mjlee consult offers tailored face to face (typically over three days including a factory/ cast house audit) and online training modules (in two to three hour blocks)
Half Day Course Why is my wire breaking?

How many wire breaks is your plant experiencing? One every 100t, 500t, 1000t...?
Why is the wire breaking? Is it a problem with my machines, procedures, raw material...the weather?
If your plant can draw one tonne of aluminium or copper with no wire breaks why not 1,000,000+ ?
This half day course draws on the broader Mine to Wire course and focuses on wire breaks delving into the source and prevention measures to move to eliminating wire breaks.
mjlee consult offers the Wire Breaks module face to face and online.Â
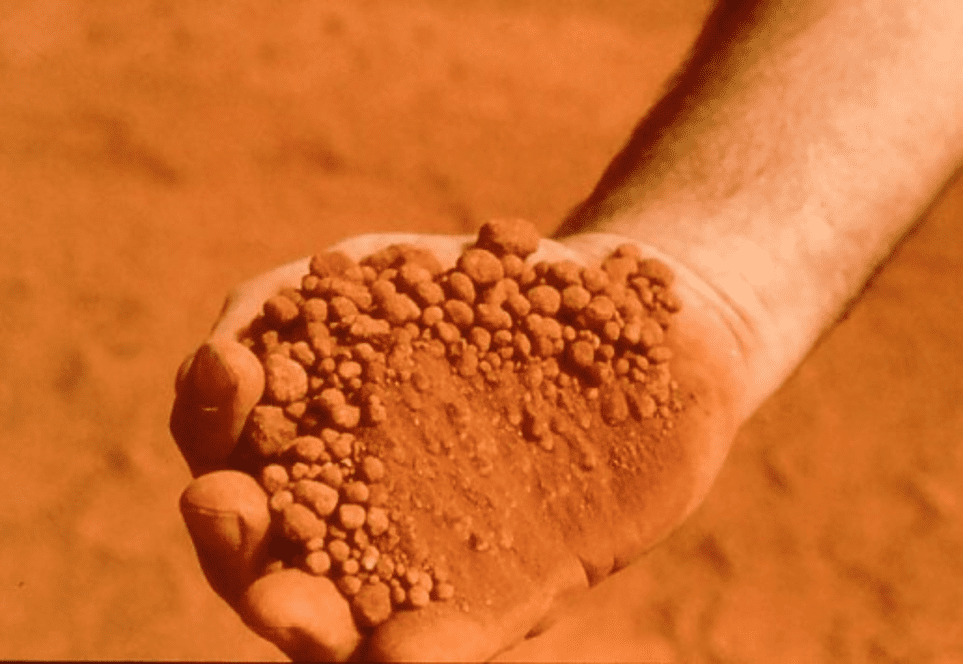
Raw Material Extraction
Mining Operations include the extraction of metals like copper and aluminium, which begins in mines where ore deposits are located. Metallurgical experts assess the quality and composition of ores to ensure suitability for conductors.
Refining and Smelting
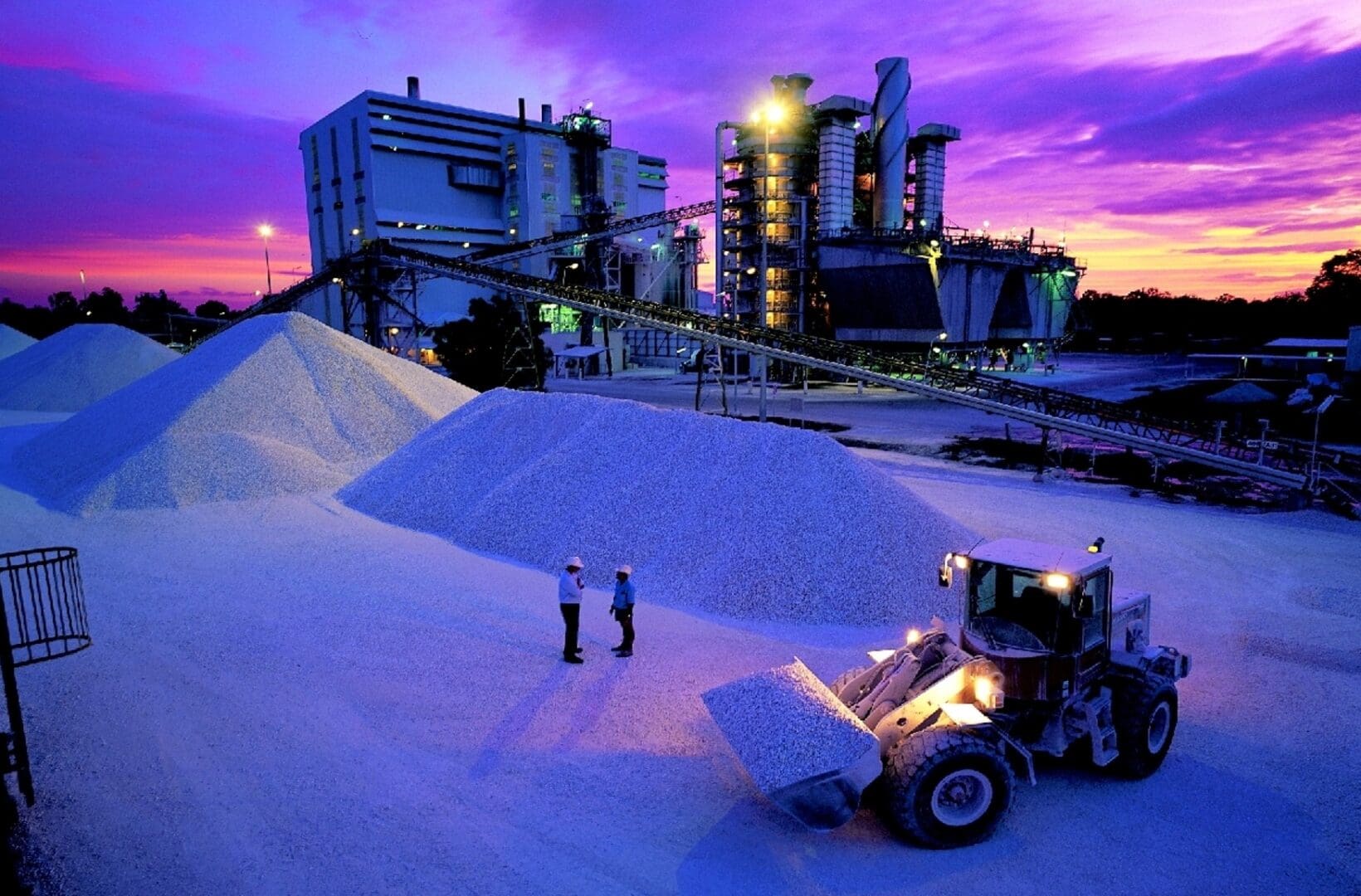
Alloying and Composition Control
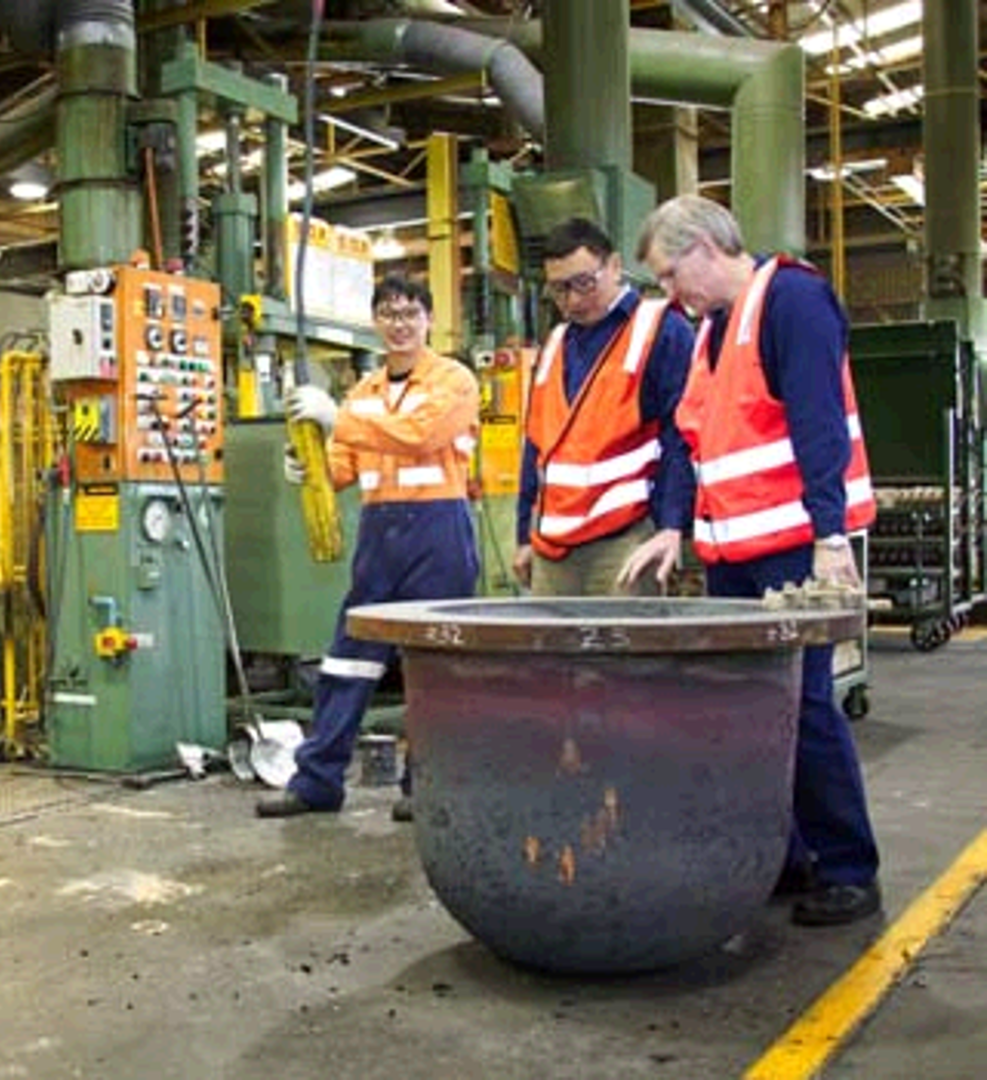

Conductor Manufacturing
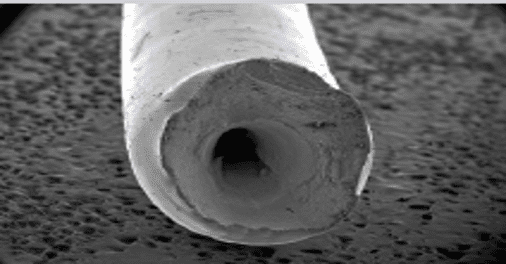
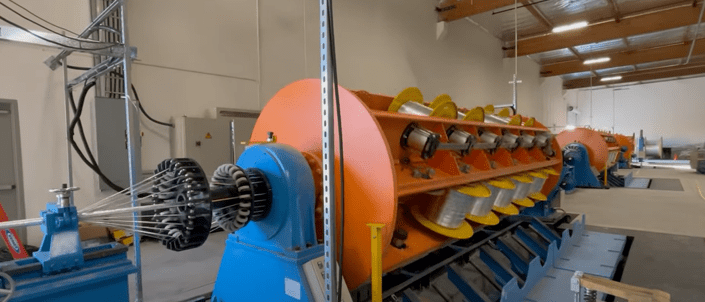
Quality Control and Testing
Final Product Manufacturing
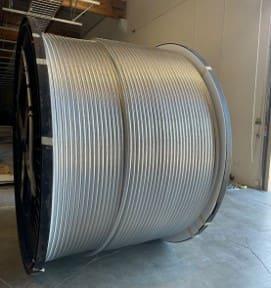

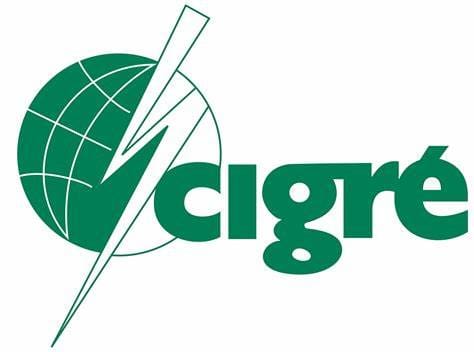
Let’s Talk
Connect with us at mjlee consult to access exclusive resources, network with like-minded individuals, and contribute to shaping the future of manufacturing advancements in the field.